What’s in your stash?
As textile artists, we enjoy working with many different fibers. The fibers available to us determine the kind of fabrics we make, giving our woven textiles the properties of strength, sheen, absorbency, durability, and drape. Cotton, linen, silk and wool have been our staples for a long time. But what’s in our stash can change as new fibers are developed, and old industries are revitalized.
Lyocell, known by the trade name Tencel ® is a relatively new fiber very popular with handweavers. It comes from wood fiber so it has the properties of absorbency and breathability associated with other cellulose fibers. It is manufactured using a similar process to rayon, where cellulose from wood pulp is liquefied, forced through a spinneret, and solidified. Lyocell is made with a closed loop process: the chemicals used in processing are reused. It has the reputation of being more eco-friendly than rayon, which is very polluting. Fabrics woven with Tencel ® are shiny and drape well, and have the advantage of being less expensive than silk.
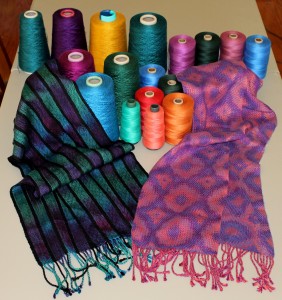
Tencel and Bamboo yarns and fabric
Bamboo yarn is also made by liquefying cellulose from pulp and then extruding the fibers in the same fashion as lyocell. There are references online to yarn spun directly from the bast fiber of bamboo, but these yarns are not easily available to handweavers. Bamboo is easy to grow and can be a sustainable resource. Fabrics woven with bamboo have amazing drape and a nice sheen.
Hemp was the most widely cultivated fiber in the world at one time. It is nice to see it making a comeback! Hemp became illegal to cultivate in this country in the 1930s, coincidentally, or not, at the same time that DuPont invented nylon. Hemp is a bast fiber, meaning it comes from the stalks of plants. Unlike the scratchy, twine-like yarns we sometimes find today, the hemp yarns of old could also be soft and have a sheen like silk. Hemp is extremely strong and durable. Yarns available to us have been coming from China and Romania, and with changing legislation we may soon see hemp yarn produced in the US.
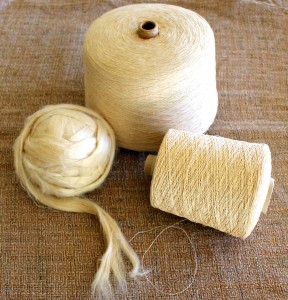
Hemp yarn and fabric
Spider silk is the strongest natural fiber known, but until now it has been very impractical to cultivate. One big problem is that spiders in captivity will eat each other. People have been fascinated with this strong, elastic fiber for a long time and have tried to figure out how to get it into production. Several attempts have been made, including genetically engineering goats to secrete the silk proteins in their milk. More recently, in Warwick Mills in New Hampshire, a caterpillar/spider crossbreed has been developed which spins this silk, appropriately called “monster silk.”
Bolt Threads in Emeryville has taken a different approach to creating a spider silk by genetically modifying and fermenting yeasts to produce similar proteins. They plan to have fabrics of this material available soon. Whether it will be used in technical applications like bulletproof vests and surgical materials, or as a fashion fiber remains to be seen.
What does the future hold for handweavers? Will the yarns on your shelf be the result of the revival of ancient agriculture, or bioengineered in a high tech lab, or both? Which fibers have the desired properties for the finished fabric? We are fortunate to have so many options available to us when we sit down at our looms.